Description
IFAN factory 30+ years manufacture experience support color /size customization support free sample.Welcome to consult for catalog and free samples.This is our Facebook Website:www.facebook.com,Click to watch IFAN’s product video.Compared with Tomex products, our IFAN products from quality to price are your best choice, welcome to buy!
High-Density Polyethylene (HDPE) fittings are essential components in modern pipeline systems. These fittings are used to connect pipes and ensure smooth fluid transportation in various industries, including water distribution, oil and gas, chemical transport, and many more. The quality of HDPE fittings plays a significant role in the long-term performance of a pipeline system. In this article, we will explore why high-quality HDPE fittings are crucial for ensuring reliability, durability, and efficiency in pipelines.
What Are HDPE Fittings?
HDPE fittings are components made from High-Density Polyethylene (HDPE) resin, designed to connect, control, or terminate the flow of liquids and gases in piping systems. These fittings are available in a variety of shapes, including elbows, tees, couplings, flanges, and more. HDPE fittings are known for their resistance to corrosion, chemicals, and extreme temperatures, making them an ideal choice for industries that rely on robust pipeline systems.
HDPE fittings are commonly used in industries such as water and wastewater management, mining, chemical transportation, and oil and gas. As the demand for durable and efficient pipeline systems increases, the importance of high-quality HDPE fittings cannot be overstated.
Why Quality HDPE Fittings Matter
1. Enhanced Durability and Reliability
One of the most important benefits of using high-quality HDPE fittings is their durability. These fittings are engineered to withstand harsh environmental conditions such as high pressure, extreme temperatures, and exposure to chemicals. Low-quality HDPE fittings may degrade over time due to poor material quality, leading to cracks, leaks, and even catastrophic system failures.
High-quality HDPE fittings are manufactured to strict industry standards and undergo rigorous testing to ensure their durability. They are designed to last for decades without the need for frequent replacements or repairs. This long-term durability ensures that pipeline systems remain reliable and efficient over time, minimizing downtime and maintenance costs.
2. Resistance to Corrosion and Chemicals
One of the key advantages of HDPE materials is their natural resistance to corrosion. Unlike traditional metal fittings, which can corrode when exposed to water, chemicals, or other corrosive substances, HDPE fittings maintain their structural integrity even in harsh environments. This is particularly important in industries like chemical manufacturing and wastewater treatment, where exposure to aggressive substances is common.
High-quality HDPE fittings are manufactured with materials that are resistant to not only corrosion but also a wide range of chemicals, including acids, alkalis, and solvents. This ensures that the fittings will continue to function effectively without the risk of contamination or system breakdowns.
3. Cost-Effectiveness
While high-quality HDPE fittings may have a higher upfront cost compared to lower-quality alternatives, they are more cost-effective in the long run. This is because high-quality fittings require less maintenance and replacement over time. Additionally, the durability and resistance to corrosion and chemicals reduce the likelihood of costly downtime and repairs.
In industries where pipeline systems are critical to business operations, minimizing the need for frequent repairs and replacements can result in significant cost savings. Investing in high-quality HDPE fittings is a wise decision that will pay off in the long term by reducing maintenance costs and increasing the lifespan of the pipeline system.
4. Enhanced Performance in High-Pressure and High-Temperature Environments
High-quality HDPE fittings are designed to perform well under high-pressure and high-temperature conditions. Many industries, such as oil and gas, require fittings that can handle extreme conditions without compromising performance. Low-quality fittings may crack or fail under pressure, leading to leaks, system failures, and even safety hazards.
Top-tier HDPE fittings are engineered to withstand high-pressure environments and maintain their integrity even in extreme temperatures. This ensures that the pipeline system operates smoothly and safely, even in challenging conditions. Whether it’s transporting hot water, steam, or pressurized chemicals, high-quality HDPE fittings are built to handle the task.
5. Easy Installation and Maintenance
Another significant advantage of using quality HDPE fittings is their ease of installation. These fittings are lightweight, easy to handle, and compatible with various welding and fusion methods, making the installation process quicker and more efficient. High-quality HDPE fittings often come with user-friendly design features that simplify the installation process, reducing labor costs and installation time.
Moreover, the low maintenance requirements of quality HDPE fittings make them a preferred choice for industries looking to minimize system downtime. With fewer repairs and replacements needed, maintenance crews can focus on other aspects of the pipeline system, resulting in better overall system performance.
Key Features of Quality HDPE Fittings
1. Fusion Capabilities
One of the defining characteristics of high-quality HDPE fittings is their fusion capabilities. Fusion welding is the process of using heat to join two HDPE pieces together, creating a permanent bond. Quality HDPE fittings are designed for optimal fusion, ensuring leak-free, strong joints that will last for decades. Proper fusion reduces the risk of joint failures and ensures the long-term integrity of the pipeline system.
2. Material Certification and Compliance
High-quality HDPE fittings are manufactured using materials that meet international industry standards, such as ASTM, ISO, and API. These fittings are subject to rigorous testing and quality control procedures to ensure that they comply with safety, performance, and environmental regulations. Ensuring that the fittings meet these certifications helps guarantee the reliability and durability of the pipeline system.
3. Customizable Designs
Many high-quality HDPE fittings can be customized to meet specific project needs. Custom fittings allow engineers to design pipeline systems that fit particular space constraints, angles, or pressure requirements. Whether it’s a custom angle, size, or material, these customizable fittings can optimize the overall performance and longevity of the pipeline system.
4. UV and Impact Resistance
HDPE fittings are naturally resistant to ultraviolet (UV) radiation and physical impacts, but high-quality versions often include additional protective coatings to further enhance these properties. UV-resistant fittings prevent degradation from prolonged exposure to sunlight, while impact-resistant designs ensure that the fittings will not crack or break under stress or external force.
How to Choose the Best HDPE Fittings for Your Project
When selecting HDPE fittings for a pipeline system, it’s important to consider several factors:
1. Application Requirements: Understand the specific needs of your pipeline system, including the type of fluids being transported, pressure, temperature, and environmental conditions.
2. Certification: Ensure that the fittings meet the relevant industry certifications and standards to guarantee their quality and performance.
3. Supplier Reputation: Choose a reputable supplier known for manufacturing high-quality HDPE fittings with a proven track record.
4. Cost vs. Value: While higher-quality fittings may cost more upfront, their long-term durability and reduced maintenance costs make them a better investment in the long run.
Conclusion
In conclusion, quality HDPE fittings are essential for the long-term performance and reliability of pipeline systems. Their resistance to corrosion, ability to withstand extreme temperatures and pressures, and ease of installation make them the ideal choice for industries requiring durable and efficient pipeline solutions. By investing in high-quality HDPE fittings, businesses can ensure the smooth operation of their pipeline systems while minimizing maintenance costs and downtime.
Frequently Asked Questions (FAQs)
1. What makes HDPE fittings durable?
HDPE fittings are durable due to their resistance to corrosion, chemicals, and extreme temperatures. They are designed to withstand harsh environmental conditions, making them long-lasting.
2. Can HDPE fittings handle high-pressure applications?
Yes, high-quality HDPE fittings are designed to handle high-pressure systems. They are built to maintain their structural integrity even under extreme pressure.
3. Are HDPE fittings environmentally friendly?
Yes, HDPE fittings are recyclable, which helps reduce their environmental impact. They are a sustainable choice for pipeline systems.
4. How long do HDPE fittings last?
With proper installation and maintenance, HDPE fittings can last up to 50-100 years, depending on environmental conditions.
5. Can I customize HDPE fittings for my project?
Yes, many manufacturers offer customizable HDPE fittings to meet the specific needs of your pipeline system, ensuring optimal performance.
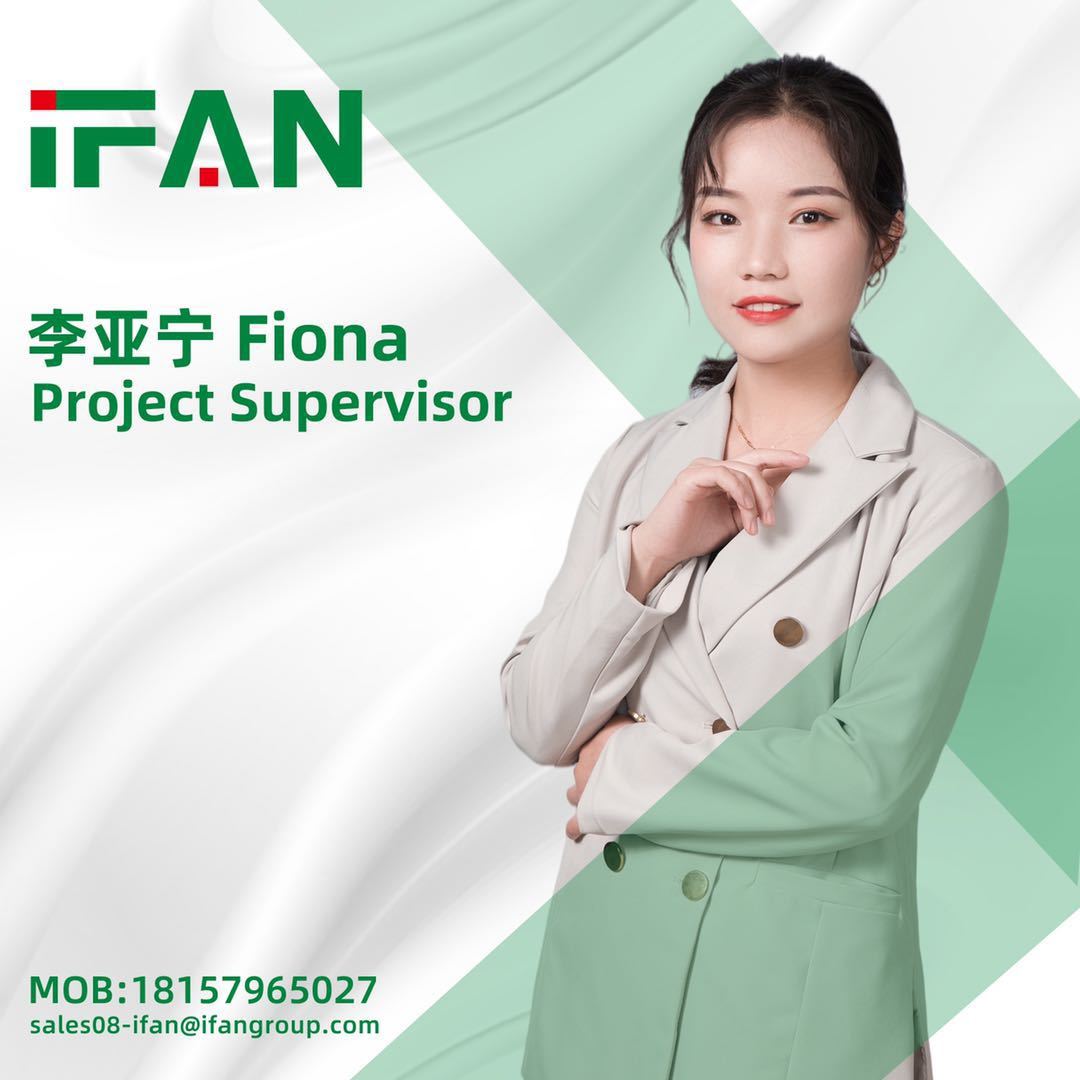