Description
IFAN factory 30+ years manufacture experience support color /size customization support free sample.Welcome to consult for catalog and free samples.This is our Facebook Website:www.facebook.com,Click to watch IFAN’s product video.Compared with Tomex products, our IFAN products from quality to price are your best choice, welcome to buy!
High-Density Polyethylene (HDPE) fittings are widely used for a variety of applications due to their durability, corrosion resistance, and cost-effectiveness. However, like any other material, HDPE fittings can experience problems over time, especially if not properly installed or maintained. In this article, we’ll explore some common **HDPE fitting problems** and provide solutions to ensure your piping system operates efficiently and lasts longer.
1. Leaking Joints
Problem:
Leaking joints are one of the most common problems with **HDPE fittings**. These leaks often occur at the connection points between pipes and fittings, typically when they haven’t been fused or installed correctly. When joints are not fused properly, it leads to a weak connection that can allow water or chemicals to leak.
Solution:
To prevent leaking joints, it’s essential to ensure that the fusion process is done properly. HDPE fittings are usually connected by a process called butt fusion or electrofusion. Both methods involve heating the surfaces of the HDPE pipes and fittings to form a secure bond once cooled. Always follow the manufacturer’s specifications for temperature, pressure, and time during the fusion process to avoid weak joints.
If a joint begins leaking after installation, the best solution is to cut out the affected section and re-fuse it properly. Using fusion machines that are well-calibrated ensures a strong, leak-free connection.
2. Cracking and Brittle Fittings
Problem:
HDPE fittings are generally resistant to environmental stress, but in some cases, exposure to extreme temperatures can cause them to crack or become brittle. This is especially common if the fittings are subjected to freezing temperatures or excessive UV exposure.
Solution:
To avoid cracking, ensure that HDPE fittings are used in environments where temperature extremes are minimal. If the system will be exposed to freezing temperatures, consider using insulation to protect the pipes and fittings. Additionally, installing UV-resistant HDPE fittings can help prevent brittleness caused by prolonged exposure to sunlight.
When replacing damaged fittings, always check the environment’s conditions and choose the appropriate HDPE grade that suits the temperature and UV exposure of the installation site.
3. Improper Installation
Problem:
Improper installation of HDPE fittings can lead to a range of issues such as misalignment, stress points, and even complete system failure. This can occur when the pipes are not adequately supported or if the fittings are not correctly aligned during installation.
Solution:
To ensure proper installation, always follow the manufacturer’s guidelines and best practices. Here are some tips for proper installation:
– Ensure that the pipes are properly aligned before fusing the fittings.
– Avoid excessive bending or stressing of the pipes during installation.
– Use proper support brackets and hangers to reduce the strain on the pipes.
– Ensure that the fusion machine is properly calibrated and maintained.
Proper training for installation technicians is also crucial to avoid mistakes that could lead to problems down the line.
4. Inadequate Pressure Handling
Problem:
HDPE fittings are designed to handle various levels of pressure. However, when subjected to pressures beyond their capacity, the fittings can become deformed or rupture. This is especially true in industrial applications where high-pressure systems are common.
Solution:
To prevent pressure-related failures, always verify the pressure ratings of the HDPE fittings you are using. HDPE fittings come in different pressure classes, so it’s important to choose fittings that match or exceed the maximum pressure requirements of the system. Additionally, make sure to regularly monitor the pressure levels in the system to avoid exceeding safe limits.
If the system requires higher pressure capabilities, it may be necessary to upgrade to fittings that are rated for more intense pressures or use additional reinforcement like steel fittings for extra strength.
5. Dirt and Contaminants
Problem:
Dirt, debris, and contaminants can accumulate inside HDPE pipes and fittings, leading to blockages, reduced flow rates, and increased pressure. These contaminants may come from the environment during installation or from the water or chemicals being transported.
Solution:
To avoid this problem, always ensure that the installation site is clean and free of dirt before laying the HDPE pipes and fittings. Additionally, ensure that cleaning procedures are followed during the installation process. Use appropriate filters to remove any debris from the transported fluid before it enters the system.
Once the system is in operation, periodic maintenance and cleaning may be necessary to ensure that the pipes remain free of contaminants. Install strainers or *ilters at critical points in the system to capture debris before it enters the piping network.
6. UV Degradation
Problem:
HDPE fittings are resistant to many environmental factors, but **UV degradation** can still occur if the pipes and fittings are exposed to sunlight for long periods. Over time, exposure to UV rays can weaken the material, causing it to crack, become brittle, or discolor.
Solution:
To protect HDPE fittings from UV degradation, ensure they are installed in areas with limited direct sunlight. For outdoor installations, choose UV-resistant HDPE fittings or apply UV protective coatings. If UV exposure is unavoidable, consider burying the pipes underground or installing UV shields to reduce direct exposure to sunlight.
7. Expansion and Contraction
Problem:
HDPE materials can expand and contract with changes in temperature, which can cause stress on fittings and joints. This movement can lead to joint failure, leakage, or even pipe misalignment.
Solution:
To address the issue of thermal expansion, allow for adequate expansion loops or space when installing HDPE fittings. This will give the pipes enough room to expand or contract without putting stress on the joints. In addition, use expansion fittings or flexible joints to accommodate any movement due to temperature changes.
Conclusion
While HDPE fittings are highly durable and resistant to many common piping issues, they are not immune to problems. Ensuring proper installation, maintaining the system regularly, and selecting the right materials for specific environmental conditions can help prevent most issues. By addressing these common problems early and taking proactive steps, you can ensure the longevity and reliability of your HDPE piping system.
Frequently Asked Questions (FAQs)
1. What are the main benefits of using HDPE fittings?
HDPE fittings offer excellent corrosion resistance, chemical resistance, flexibility, and long-lasting durability, making them ideal for water, gas, and industrial applications.
2. How can I prevent leaks in HDPE fittings?
Proper fusion of the pipes and fittings is essential to prevent leaks. Ensure the fusion process is done correctly according to manufacturer guidelines.
3. Can HDPE fittings withstand high-pressure systems?
Yes, HDPE fittings are available in different pressure ratings, so it’s important to choose the correct fittings for the system’s pressure requirements.
4. How do I protect HDPE fittings from UV degradation?
Use UV-resistant HDPE fittings or apply UV protective coatings if the fittings will be exposed to direct sunlight for extended periods.
5. What should I do if an HDPE fitting starts cracking?
If cracking occurs, replace the damaged fitting and check the environmental conditions (such as temperature and UV exposure) to prevent future issues.
Related products
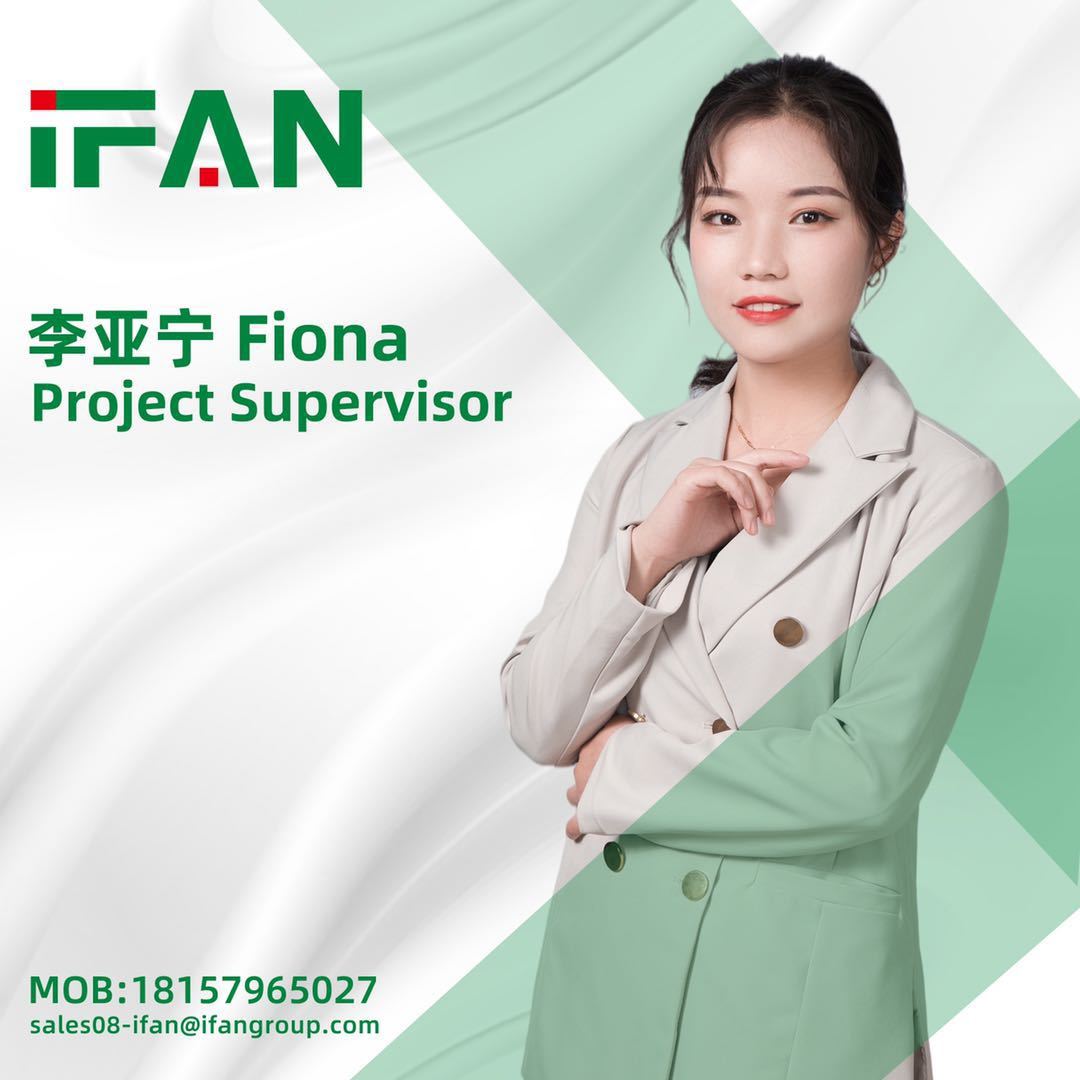