Description
IFAN factory 30+ years manufacture experience support color /size customization support free sample.Welcome to consult for catalog and free samples.This is our Facebook Website:www.facebook.com,Click to watch IFAN’s product video.Compared with Tomex products, our IFAN products from quality to price are your best choice, welcome to buy!
High-Density Polyethylene (HDPE) fittings are critical components used in a wide range of industries, especially in water, gas, and oil distribution systems. As demand for more efficient, durable, and cost-effective solutions grows, innovations in HDPE fitting design have become key to meeting these challenges. This article explores the latest advancements in HDPE fitting design, how they enhance system performance, and why these innovations are a game-changer for various industries.
What are HDPE Fittings?
HDPE fittings are components designed to connect, control, or terminate the flow of fluids through HDPE (High-Density Polyethylene) pipes. These fittings come in various shapes and sizes, and they are known for their robustness, ease of installation, and resistance to corrosion. Due to these characteristics, HDPE fittings are particularly valuable in environments exposed to harsh chemicals, extreme temperatures, and high pressures, which are common in the oil and gas, water management, and utilities industries.
Why Innovations in HDPE Fitting Design Matter
1. Improved Durability
Traditional metal fittings often degrade over time due to exposure to corrosive substances, making maintenance a major issue. HDPE fittings, on the other hand, are naturally resistant to corrosion, making them an excellent choice for pipelines carrying aggressive chemicals or exposed to harsh environmental conditions. However, innovations in HDPE fitting designs have enhanced their durability even further, allowing them to withstand more extreme conditions than before.
2. Enhanced Performance in Extreme Conditions
The oil and gas industry, as well as industries dealing with chemicals, face challenges such as extreme temperatures, high pressures, and constant movement of the pipeline. Innovations in HDPE fitting design now allow these fittings to better perform under these harsh conditions. The new designs feature enhanced pressure ratings, and the ability to resist cracking and breaking in fluctuating temperature extremes. This leads to improved reliability and longer service life for pipeline systems.
3. Better Compatibility with Modern Pipelines
As the demand for more flexible and high-performance pipelines grows, HDPE fitting designs have evolved to integrate seamlessly with newer HDPE piping systems. Innovations now include designs that offer better fusion capabilities, resulting in smoother connections, fewer weak points, and stronger joints, which ultimately help minimize leaks and maximize the efficiency of pipeline systems.
4. Cost-Effective and Efficient Installation
The design innovations in HDPE fittings not only improve their functionality but also streamline the installation process. With easier-to-handle components, labor costs are reduced. HDPE fittings require fewer tools and less specialized labor compared to traditional metal fittings, further lowering the overall cost of installation. Additionally, the lightweight nature of HDPE fittings means they are easier to transport, which is especially important in remote locations or difficult terrains.
5. Sustainability and Environmental Benefits
With growing environmental concerns, the design of HDPE fittings has shifted towards increasing their sustainability. HDPE materials are recyclable, reducing the carbon footprint of pipelines. New designs focus on minimizing waste during manufacturing, leading to more efficient use of resources. Additionally, innovations in HDPE fitting design ensure a longer lifespan, which reduces the need for frequent replacements and decreases environmental impact.
Key Innovations in HDPE Fitting Design
1. Fusion Technology Improvements
Fusion welding, the method used to join HDPE pipes and fittings, has undergone significant advancements. New fusion technologies enable stronger, more durable bonds, reducing the risk of leaks and joint failures. Innovations such as electrofusion and butt fusion allow for more precise and efficient connections, ensuring a stronger, leak-free system. This technology has improved installation speed and reduced errors, making it one of the most significant design innovations in HDPE fitting manufacturing.
2. Smart Fittings with Monitoring Capabilities
One of the most exciting innovations in HDPE fitting design is the integration of smart technology. With built-in sensors and monitoring capabilities, these smart HDPE fittings can track pressure, temperature, and flow rate in real-time. This allows for proactive maintenance and immediate detection of any irregularities, preventing leaks and system failures before they occur. Such innovations make pipelines more efficient and reduce downtime, ultimately improving system performance and longevity.
3. Enhanced Structural Reinforcement
Innovations in material science have led to the development of HDPE fittings with enhanced structural reinforcement. These new fittings offer improved resistance to external pressures, such as those found in subsea installations or in regions prone to earthquakes. Reinforced HDPE fittings are also more impact-resistant, meaning they are less likely to suffer damage from external forces like construction or natural events. These advancements make HDPE fittings ideal for use in a wide range of industries where strength and durability are crucial.
4. Customizable Fitting Designs
Today, manufacturers offer customizable HDPE fittings to meet specific system requirements. Whether it’s a unique angle, size, or material, custom-designed fittings ensure that the pipeline systems are optimally constructed. This flexibility is particularly beneficial for industries such as oil and gas, where pipelines often need to navigate difficult terrains or unusual system specifications. Custom designs also allow for more efficient use of space and resources, optimizing the overall pipeline layout.
5. Corrosion-Resistant Coatings and Linings
While HDPE is naturally resistant to corrosion, recent innovations have introduced specialized coatings and linings that further enhance this property. These coatings increase resistance to specific chemicals and further protect HDPE fittings in extreme environments. In some cases, the coatings also improve UV resistance, ensuring HDPE fittings maintain their structural integrity when exposed to sunlight for prolonged periods. Such innovations contribute to the long lifespan of HDPE fittings, reducing the need for replacements and costly maintenance.
Applications of Innovative HDPE Fitting Designs
1. Water Distribution Systems
With new advancements, HDPE fittings are becoming the preferred choice for water distribution systems. The combination of cost-effectiveness, ease of installation, and the ability to withstand high pressures and temperatures makes them a popular choice for municipal and industrial water supply systems. Innovations in design also make HDPE fittings more efficient at managing water flow, reducing leaks and improving system performance.
2. Oil and Gas Pipelines
The oil and gas industry benefits immensely from innovative HDPE fitting designs, especially in offshore and subsea pipeline installations. With improved pressure and temperature resistance, these fittings help ensure the integrity of pipeline systems that transport oil, gas, and other fluids across vast distances. The increased durability and reduced risk of corrosion make HDPE fittings ideal for challenging environments.
3. Chemical Transportation
HDPE fittings are used extensively in the chemical industry, where they transport a variety of aggressive chemicals. With innovations in HDPE design, these fittings are now more resistant to the corrosive effects of chemicals, ensuring that they last longer and function more efficiently.
4. Industrial Applications
Innovative HDPE fittings are also making their way into industrial applications, such as power plants and manufacturing facilities. Their ability to handle high temperatures, chemicals, and physical stress makes them essential for maintaining the reliability of industrial systems.
Conclusion
Innovations in HDPE fitting design have revolutionized the way pipeline systems are constructed and maintained. With increased durability, better performance in extreme conditions, improved installation processes, and sustainability benefits, HDPE fittings are more efficient and cost-effective than ever before. As industries continue to face growing demands for safer, more reliable pipeline systems, these innovations ensure that HDPE fittings remain an essential component for years to come.
Frequently Asked Questions (FAQs)
1. What is the lifespan of HDPE fittings?
HDPE fittings are designed to last for 50 to 100 years, depending on environmental conditions and how well they are maintained.
2. Can HDPE fittings handle high-pressure systems?
Yes, HDPE fittings are suitable for high-pressure applications, and the design innovations have enhanced their pressure resistance even further.
3. Are there smart HDPE fittings with monitoring capabilities?
Yes, modern HDPE fittings come with integrated sensors that allow for real-time monitoring of pressure, temperature, and flow rate.
4. How do HDPE fittings perform in extreme temperatures?
HDPE fittings are highly resistant to extreme temperatures, with many designs able to withstand temperatures from -40°C to 60°C without cracking.
5. Are HDPE fittings environmentally friendly?
Yes, HDPE fittings are recyclable and designed for long-term use, which reduces waste and their environmental impact.
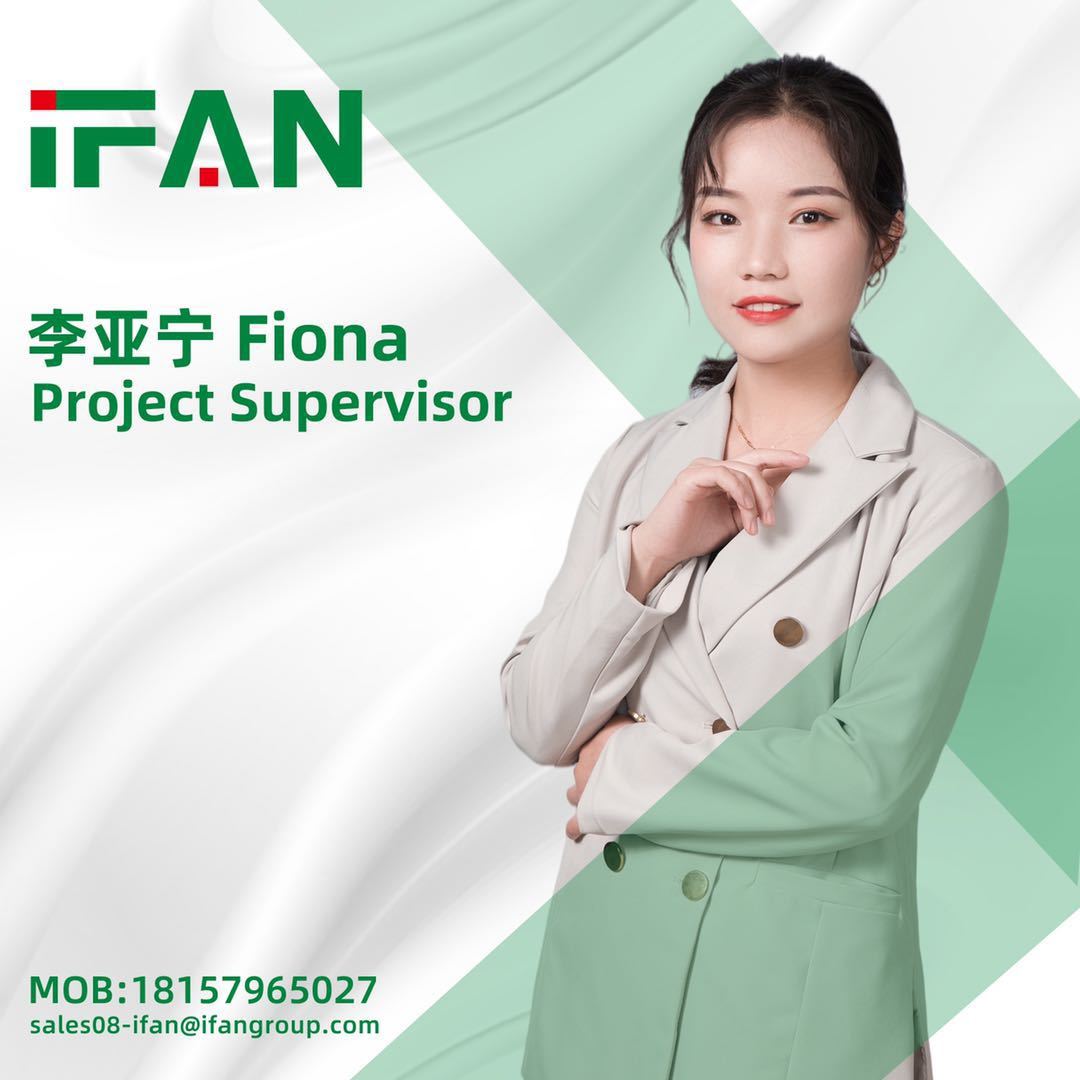