Brass valves are widely used in various industries and applications due to their durability, reliability, and resistance to corrosion. The manufacturing process of brass valves involves several steps, each contributing to the final product’s quality and functionality. In this overview, we will explore the key stages involved in the production of brass valves. Let’s break down each aspect into separate sections.
1. Material Selection
The first step in manufacturing brass valves is selecting the appropriate materials. Brass, an alloy of copper and zinc, is the primary material used. The specific composition of the brass alloy will depend on the desired properties of the valve, such as strength, corrosion resistance, and machinability.
2. Casting
The casting process involves melting the selected brass alloy and pouring it into a mold. The mold is typically made of sand or metal and is designed to create the desired shape and structure of the valve. Once the molten brass cools and solidifies, the mold is removed, leaving behind the rough shape of the valve.
3. Machining
After casting, the rough valve undergoes machining to achieve its final size and shape. This process involves using precision tools, such as lathes, drills, and milling machines, to remove excess material and create the necessary features, such as threads, sealing surfaces, and connections.
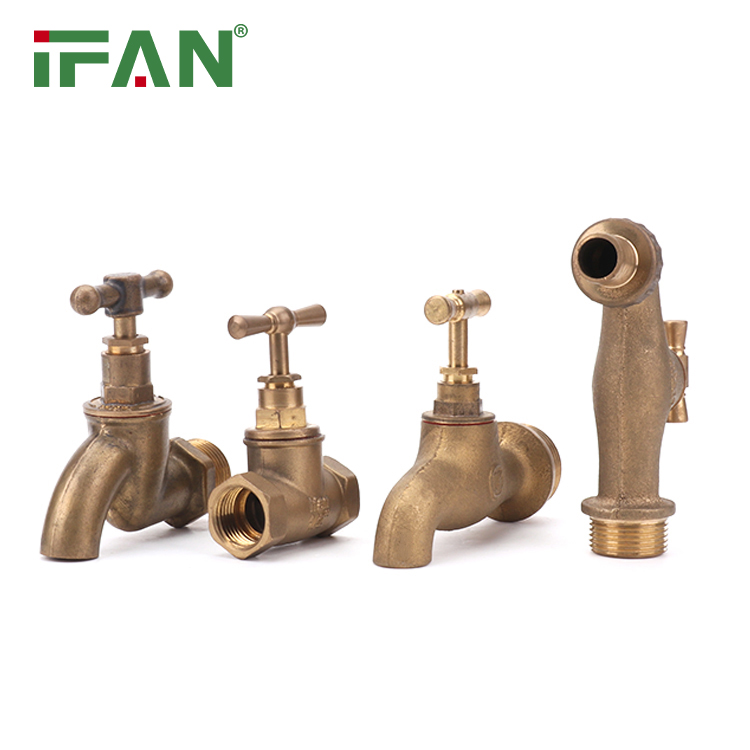
4. Assembly
Once the individual components of the valve have been machined, they are assembled together. This may involve joining the body, stem, ball, and other parts using techniques such as threading, soldering, or welding. Seals, such as O-rings or gaskets, are also incorporated at this stage to ensure proper sealing and prevent leaks.
5. Surface Treatment
To enhance the valve’s appearance and protect it from corrosion, various surface treatments may be applied. Common surface treatments for brass valves include polishing, plating, or coating. Polishing helps achieve a smooth and visually appealing surface, while plating or coating, such as chrome or nickel plating, provides a protective layer against corrosion.
6. Quality Control
Throughout the manufacturing process, strict quality control measures are implemented to ensure that the valves meet industry standards and customer requirements. This may involve performing inspections, tests, and measurements to check for dimensional accuracy, functionality, and leak-tightness. Defective valves are identified and rejected to maintain the highest quality standards.
Conclusion
The manufacturing of brass valves involves a series of steps, from material selection to quality control. The casting and machining processes shape the rough valve, which is then assembled, treated, and inspected to create the final product. The careful selection of materials, precision machining, and surface treatments contribute to the durability, reliability, and corrosion resistance of brass valves. Through these manufacturing processes, brass valves are able to meet the diverse needs and demands of various industries and applications.
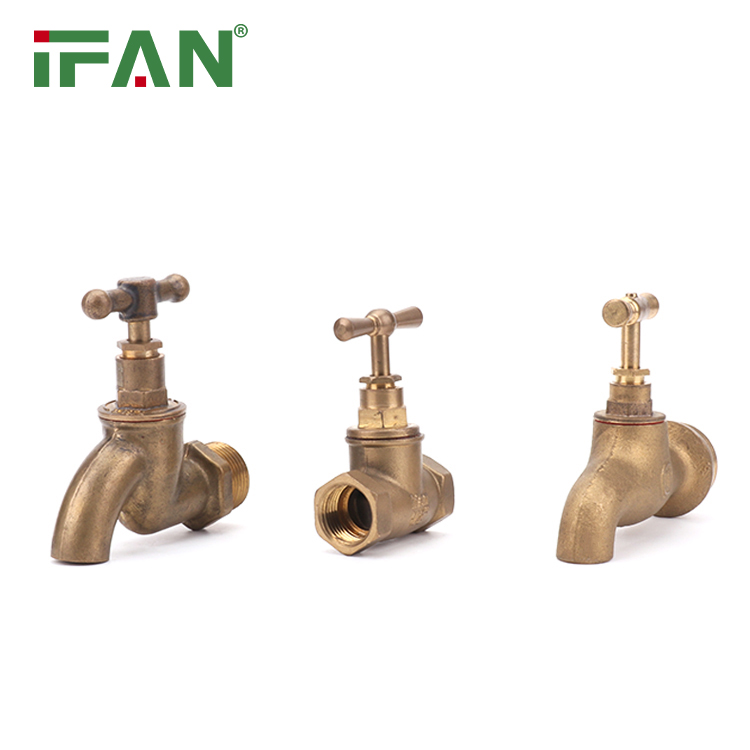