Exploring the Manufacturing Process of PPR Fiberglass Pipes
PPR (Polypropylene Random Copolymer) fiberglass pipes are manufactured using a meticulous process that combines PPR material with fiberglass reinforcement. This process results in pipes that offer exceptional durability, longevity, and other desirable properties. In this comprehensive overview, we will explore the key steps involved in the manufacturing process of PPR fiberglass pipes. Let’s break down each step into separate sections.
1. Material Preparation
The manufacturing process begins with the preparation of the PPR material. Polypropylene, a thermoplastic polymer, is melted and mixed with various additives, including stabilizers and colorants, to enhance its performance and appearance. The resulting mixture is extruded into granules or pellets, which serve as the base material for PPR pipes.
2. Fiberglass Reinforcement
Next, fiberglass reinforcement is incorporated into the PPR material. Fine strands of glass fibers are blended with the molten PPR material, forming a composite mixture. The fiberglass reinforcement provides added strength, rigidity, and resistance to external pressures and impacts.
3. Pipe Extrusion
The composite blend is then fed into an extrusion machine during the pipe extrusion stage. The machine heats the material to a molten state and forces it through a die, shaping it into the desired pipe diameter and thickness. The extruded pipe is rapidly cooled to solidify it and ensure its structural integrity.
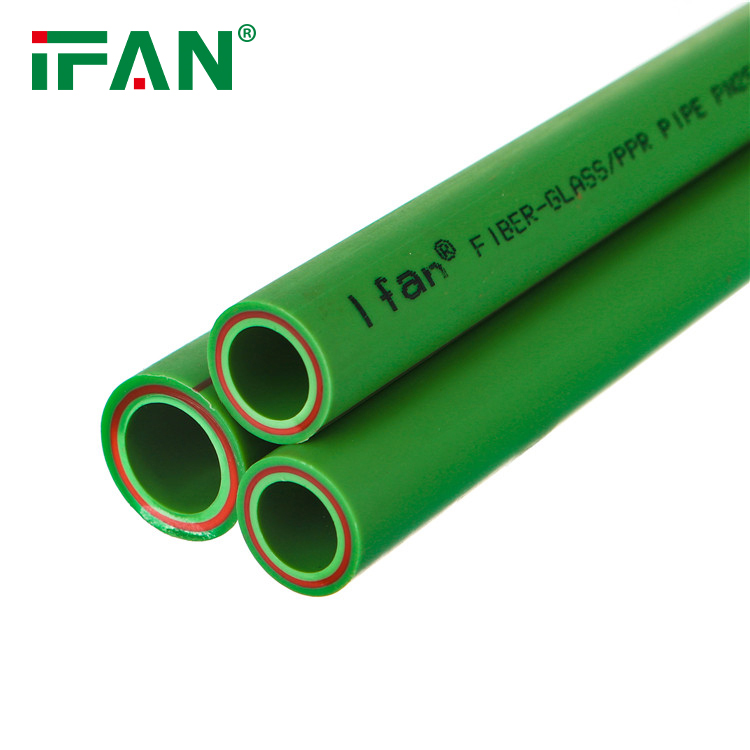
4. Pipe Sizing and Shaping
After extrusion, the pipe passes through a series of sizing and shaping tools. These tools help control the dimensions and roundness of the pipe, ensuring it has a smooth and uniform inner and outer surface. This smooth surface promotes efficient fluid flow and minimizes pressure losses.
5. Heat Fusion
PPR fiberglass pipes are connected using heat fusion techniques to create strong and leak-free joints. The ends of the pipes are heated using a specialized fusion tool, raising the temperature of the PPR material to its melting point. The heated ends are then pressed together, allowing the molten material to fuse and form a solid, homogeneous joint. Heat fusion creates connections that are highly reliable, durable, and resistant to leakage.
6. Quality Control
Throughout the manufacturing process, stringent quality control measures are implemented to ensure the PPR fiberglass pipes meet specified standards. The pipes undergo inspection for dimensional accuracy, smoothness of the inner surface, and overall visual appearance. Mechanical tests, such as pressure resistance and impact strength tests, are conducted to verify the pipes’ performance under different conditions.
7. Packaging and Distribution
Once the PPR fiberglass pipes pass the quality control tests, they are packaged and prepared for distribution. The pipes are carefully bundled and protected to prevent damage during transportation. Proper labeling and documentation are provided to ensure accurate identification and traceability.
Conclusion
The manufacturing process of PPR fiberglass pipes involves precise steps, including material preparation, fiberglass reinforcement, pipe extrusion, sizing and shaping, heat fusion, and quality control. This meticulous process ensures the production of high-quality pipes that exhibit exceptional durability, longevity, and other desirable properties. By understanding the manufacturing process of PPR fiberglass pipes, users can appreciate the craftsmanship involved and have confidence in the performance and reliability of these pipes in various applications.
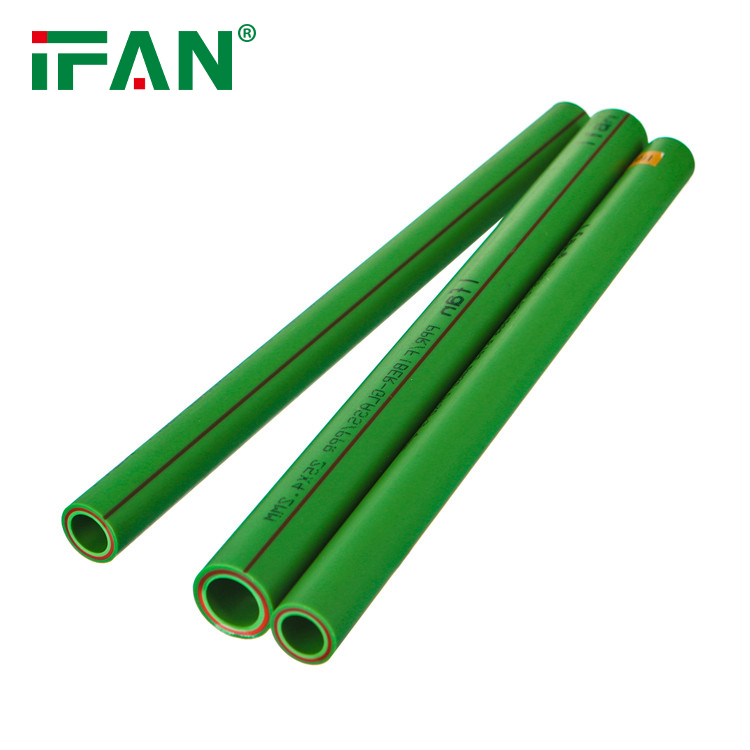