Common Installation Methods for PPR Fiberglass Pipes
Introduction
PPR (Polypropylene Random Copolymer) fiberglass pipes are widely used in various applications due to their excellent properties and durability. Proper installation is crucial to ensure the integrity and efficiency of the piping system. In this article, we will explore some of the common installation methods for PPR fiberglass pipes. Let’s break down each section into separate headings.
1. Socket Fusion Welding
Socket fusion welding is one of the most common installation methods for PPR fiberglass pipes. It involves using a specialized fusion tool to heat the end of the pipe and the socket fitting simultaneously. Once the desired temperature is reached, the pipe and fitting are quickly joined together, creating a strong and leak-proof connection. Socket fusion welding is relatively simple and requires minimal tools, making it a popular choice for both professional installers and do-it-yourself projects.
2. Electrofusion Welding
Electrofusion welding is another commonly used installation method for PPR fiberglass pipes, especially for larger diameter pipes. This method involves using specialized electrofusion fittings that have built-in resistance wires. The fittings are placed on the pipe ends, and an electrofusion welding machine is used to pass a controlled electrical current through the wires, heating and melting the fitting and pipe material. As the materials cool, they fuse together, forming a strong and durable joint. Electrofusion welding ensures a reliable and uniform connection, particularly for pipes carrying high-pressure fluids.
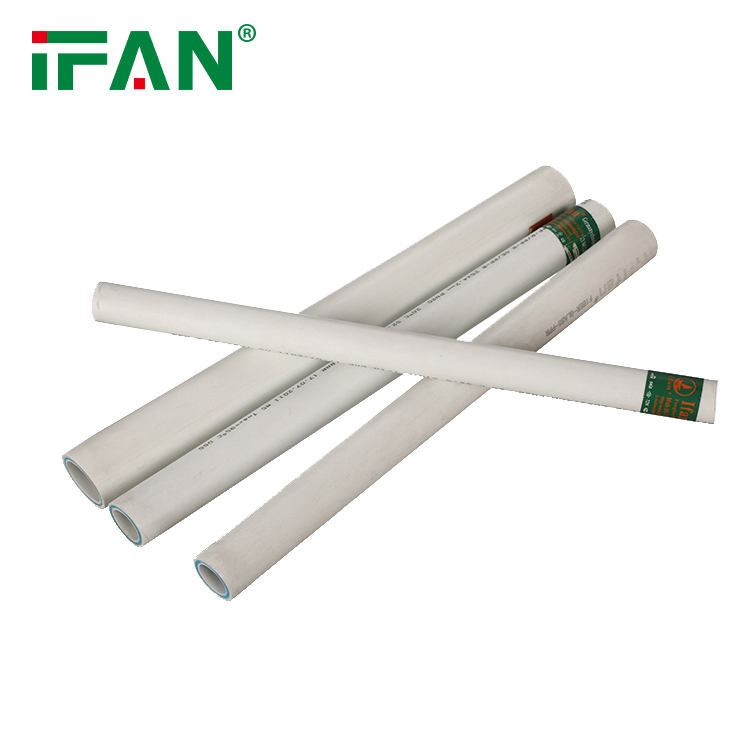
3. Mechanical Joints
Mechanical joints provide an alternative installation method for PPR fiberglass pipes, offering flexibility and ease of disassembly if needed. These joints utilize fittings, such as compression fittings or push-fit fittings, that do not require heat or welding for installation. Compression fittings involve applying pressure to the fitting using a nut and compression ring, tightly securing the pipe in place. Push-fit fittings, on the other hand, utilize a rubber or EPDM O-ring to create a watertight seal when the pipe is inserted into the fitting. Mechanical joints are suitable for applications where frequent modifications or disassembly may be required.
4. Butt Fusion Welding
Butt fusion welding is commonly used for larger diameter PPR fiberglass pipes in industrial applications. This method involves heating the pipe ends simultaneously using specialized butt fusion welding equipment. Once the pipe ends reach the appropriate melting temperature, they are brought together and pressed firmly, allowing the materials to fuse together as they cool. Butt fusion welding provides a strong and seamless joint, ensuring efficient fluid flow and resistance to high pressure and temperature conditions.
5. Horizontal Directional Drilling
In situations where trenching is not feasible or desirable, horizontal directional drilling (HDD) can be employed to install PPR fiberglass pipes underground. HDD involves using specialized equipment to drill a small pilot hole horizontally underground. The PPR fiberglass pipe is then pulled through the hole, following the path created by the drilling equipment. HDD allows for minimal disruption to the surface and is commonly used for installing pipes under roadways, rivers, or environmentally sensitive areas.
Conclusion
Proper installation is crucial for the successful operation of PPR fiberglass pipes. The common installation methods include socket fusion welding, electrofusion welding, mechanical joints, butt fusion welding, and horizontal directional drilling. Each method offers its own advantages and is suitable for different applications and project requirements. By choosing the appropriate installation method and following industry best practices, the integrity, reliability, and efficiency of PPR fiberglass pipe systems can be upheld, ensuring long-term performance and cost-effectiveness.
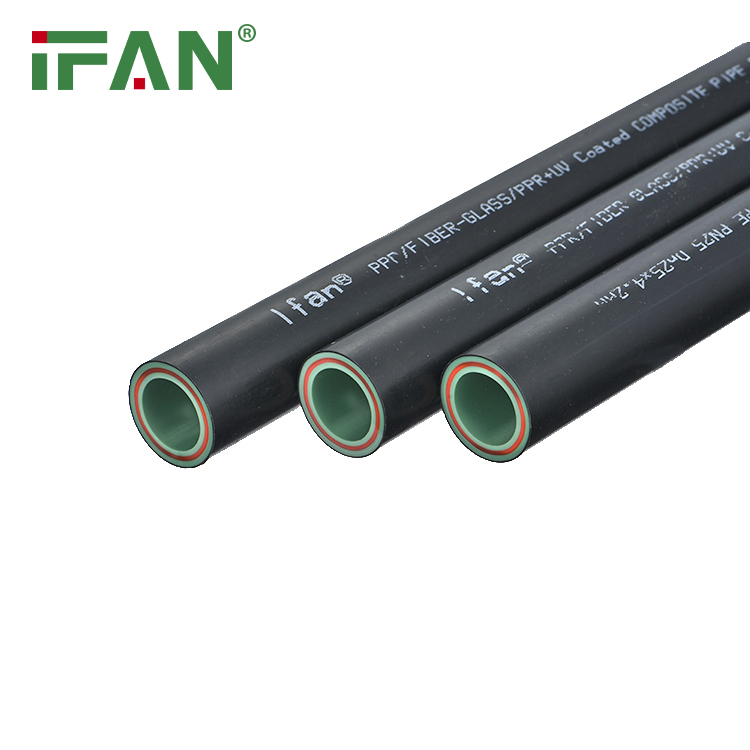