What is HDPE Pipe Fittings: Understanding the Basics
HDPE (high-density polyethylene) pipe fittings are integral components used in piping systems to connect, control, and redirect the flow of fluids or gases. This comprehensive overview will provide a clear understanding of HDPE pipe fittings, their construction, benefits, applications, and the importance of proper installation.
Construction of HDPE Pipe Fittings
HDPE pipe fittings are typically made from high-density polyethylene material, known for its exceptional strength, flexibility, and chemical resistance. These fittings are manufactured using various techniques, including injection molding or extrusion, to create a wide range of shapes and sizes to suit different piping needs.
- Design: HDPE fittings are designed to provide a secure and leak-free connection between HDPE pipes. They feature a variety of shapes and configurations, such as elbows, tees, reducers, couplers, and flanges, to accommodate different installation requirements.
- Material: HDPE pipe fittings are made from the same high-density polyethylene material as the pipes they connect. This ensures compatibility, uniformity, and consistent performance throughout the piping system.
- Joints: HDPE fittings utilize different jointing methods to connect pipes, including fusion techniques (butt fusion, electrofusion) and mechanical methods (compression fittings). These joints ensure a strong, reliable, and long-lasting connection.
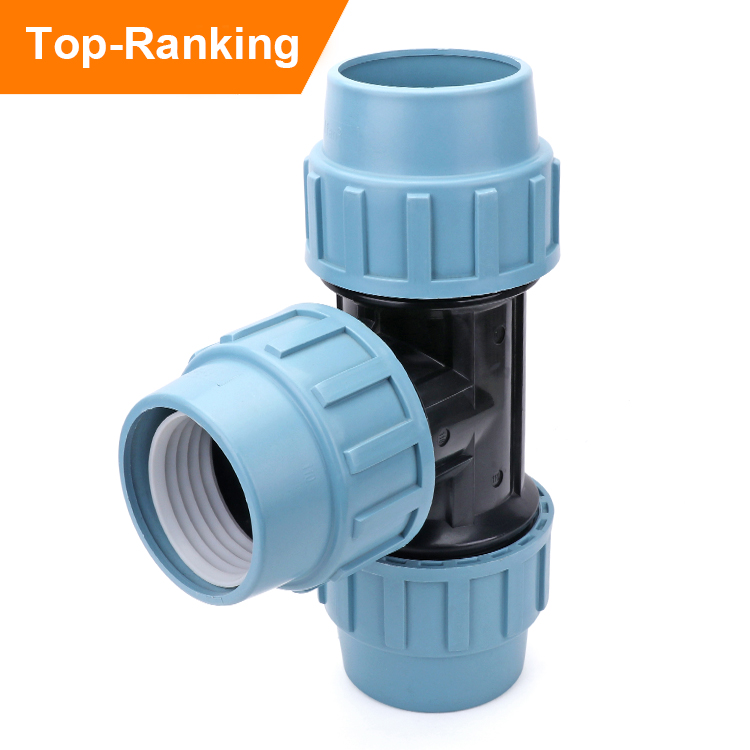
Benefits of HDPE Pipe Fittings
HDPE pipe fittings offer numerous advantages that contribute to their widespread use in various industries and applications:
- Durability: HDPE fittings are highly resistant to corrosion, chemicals, and UV degradation, providing long-term durability and reliability in harsh environments.
- Flexibility: HDPE fittings can withstand significant bending and twisting without breaking or deforming, allowing for easy installation around obstacles and reducing the need for additional fittings.
- Chemical Resistance: HDPE pipe fittings exhibit excellent resistance to a wide range of chemicals, making them suitable for handling corrosive fluids or gases.
- Leak-Free Joints: Fusion joints provide seamless and leak-free connections, ensuring the integrity of the piping system and minimizing the risk of leakage.
- Low Maintenance: HDPE fittings require minimal maintenance due to their resistance to corrosion, chemical attack, and abrasion. This reduces the overall lifecycle costs of the piping system.
Applications of HDPE Pipe Fittings
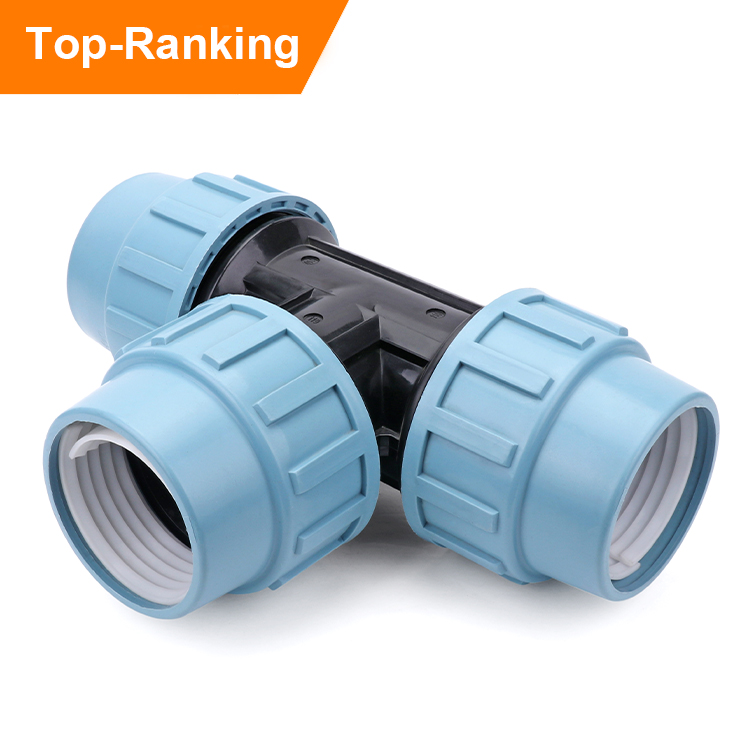
HDPE pipe fittings find applications in various industries and sectors due to their versatility, reliability, and compatibility with different fluids and gases. Some common applications include:
- Water Supply Systems: HDPE fittings are widely used in water distribution networks for municipal, commercial, and residential applications, providing a reliable and safe flow of potable water.
- Gas Distribution Networks: HDPE fittings are commonly employed in gas distribution systems, ensuring a secure and leak-free transport of natural gas or other gases.
- Industrial Piping: HDPE fittings are suitable for industrial applications, including chemical processing, mining, wastewater treatment, and irrigation systems. They provide a robust and corrosion-resistant solution for fluid and gas handling.
- Landfill and Environmental Applications: HDPE fittings are utilized in landfill liner systems, drainage systems, and environmental remediation projects due to their resistance to chemicals and ability to handle aggressive substances.
Importance of Proper Installation
Proper installation of HDPE pipe fittings is crucial to ensure the optimal performance and longevity of the piping system:
- Qualified Installers: HDPE fittings should be installed by trained professionals who have expertise in fusion techniques or mechanical joining methods. Improper installation can lead to leaks, joint failure, or compromised system integrity.
- Quality Control: It is essential to follow the manufacturer’s guidelines and industry standards to ensure the correct fusion parameters, pressures, and temperatures are maintained during the installation process.
- Inspection and Testing: After installation, the joints should be thoroughly inspected for proper alignment, fusion quality, and overall integrity. Pressure testing can be conducted to verify the system’s reliability and identify any potential issues.
Conclusion
HDPE pipe fittings play a critical role in connecting and controlling fluid or gas flow in piping systems. With their durable construction, flexibility, chemical resistance, and leak-free joints, HDPE fittings provide reliable and long-lasting solutions across diverse applications. Proper installation by qualified professionals ensures optimal performance and system integrity. By understanding the basics of HDPE pipe fittings, one can make informed decisions regarding their selection, installation, and maintenance, ultimately ensuring the success of the piping system.