IFAN factory 30+ years manufacture experience support color /size customization support free sample.Welcome to consult for catalog and free samples.This is our Facebook Website:www.facebook.com,Click to watch IFAN’s product video.Compared with Tomex products, our IFAN products from quality to price are your best choice, welcome to buy!
1. Material Selection and Preparation
The manufacturing process of brass fittings begins with the careful selection and preparation of materials. Brass, an alloy primarily composed of copper and zinc, can be customized with varying proportions of these elements and additional metals such as lead or tin to achieve desired properties. The selection of materials depends on the intended application and performance requirements of the fittings. Once selected, the brass is melted in a furnace, mixed to the desired composition, and then cast into ingots or billets. These preliminary forms are subsequently cooled and prepared for further processing.
2. Casting and Forging
Casting and forging are two primary methods used in the production of brass fittings. In the casting process, molten brass is poured into molds to form the basic shape of the fittings. This method is suitable for producing complex shapes and large quantities. For more precise and high-strength components, forging is employed. In forging, heated brass billets are mechanically deformed using hammers or presses to shape the fittings. Forging enhances the mechanical properties of the brass, resulting in stronger and more durable fittings. Both methods have their advantages and are chosen based on the specific requirements of the fittings.
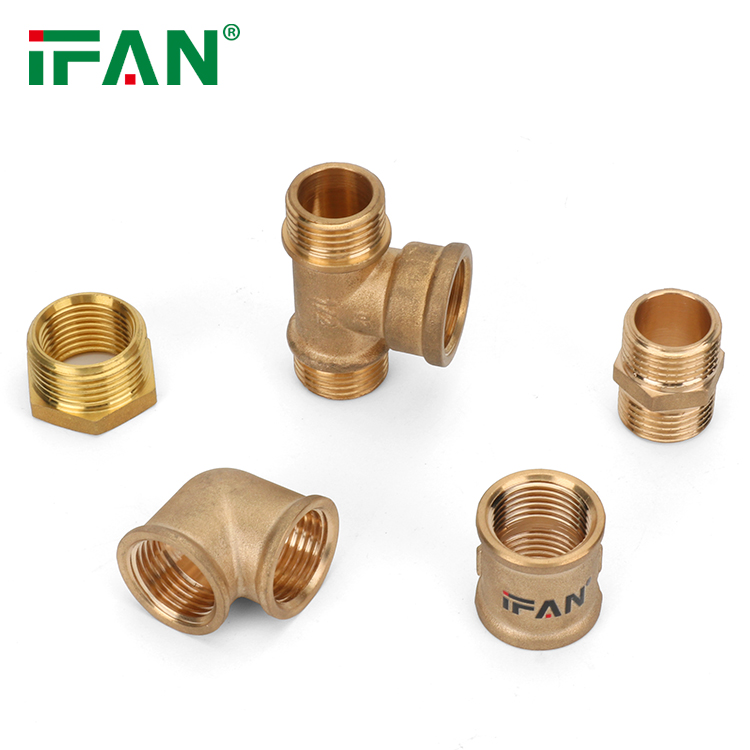
3. Machining and Fabrication
Once the initial shape of the brass fittings is achieved through casting or forging, they undergo machining and fabrication processes. Machining involves removing excess material using tools like lathes, mills, or drills to achieve precise dimensions and surface finishes. This step is crucial for ensuring that the fittings meet tight tolerances and functional requirements. Fabrication processes may also include threading, drilling, or milling to add specific features required for the fitting’s functionality. This stage ensures that the fittings are ready for assembly and installation in their intended applications.
4. Surface Treatment and Finishing
Surface treatment and finishing are critical steps in the manufacturing process of brass fittings, as they enhance both appearance and performance. Various techniques are used to improve the surface quality and protect against corrosion. Common treatments include polishing to achieve a smooth, shiny finish, and coating with protective layers such as lacquer or electroplating. Electroplating, often with materials like nickel or chromium, provides a barrier against corrosion and wear. Additionally, surface treatments may include passivation, which helps to improve the corrosion resistance of the brass by removing contaminants and enhancing the protective oxide layer.

5. Quality Control and Testing
Quality control and testing are essential to ensure that brass fittings meet the required standards and specifications. During and after manufacturing, fittings are subjected to various tests to verify their performance, strength, and durability. Common tests include dimensional inspections, pressure tests, and material analysis. Dimensional inspections ensure that the fittings conform to design specifications, while pressure tests check for leaks and structural integrity. Material analysis assesses the composition and properties of the brass to confirm that it meets quality standards. These rigorous quality control measures help prevent defects and ensure that the fittings perform reliably in their applications.
In conclusion, the manufacturing process of brass fittings involves several critical stages, including material selection, casting or forging, machining, surface treatment, and quality control. Each stage plays a vital role in ensuring the production of high-quality, durable fittings that meet specific application requirements. By understanding these processes, one can appreciate the complexity and precision involved in creating brass fittings and the importance of each step in achieving optimal performance and reliability.